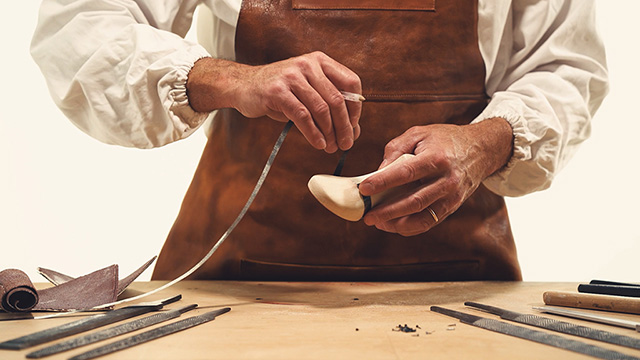
Of Quality and Excellence
Consisting out of more than 45 pieces, and more than 110 individual operations, every single shoe is crafted with meticulous attention to detail. The skill of numerous craftsmen is required, each having mastered a particular step in the process in order to fashion a pair of shoes.
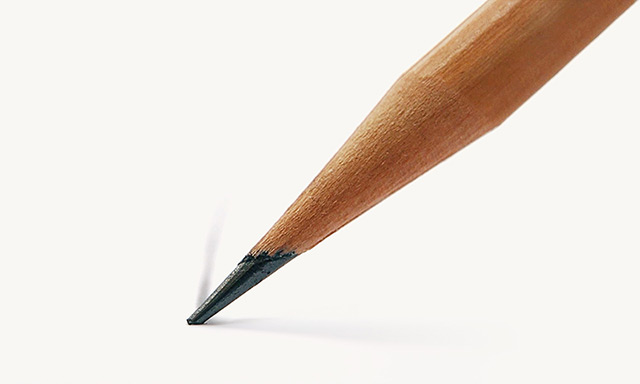
Italian Design
It all starts with a spark of imagination. In our Italian Design Lab, inspiration flows from mind to paper creating the concept of a unique design. Entirely drawn by hand yet taking the correct measurements into account, an exceptional combination between artistry and mathematics takes place.
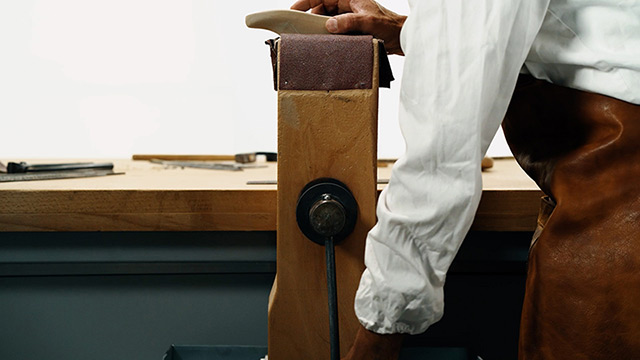
Wooden Last
Simultaneously, an initial wooden last is shaped from hornbeam wood by a skilled last maker, the "modellista forme". The last mimics the outlines of a specific foot-size around which the shoe will be crafted, determining the final shape of the shoe.
Once all modifications are finalized, the wooden last is transformed into an even more durable manufacturing last. These can be re-used multiple times and even resmelted to make new ones almost indefinitely.
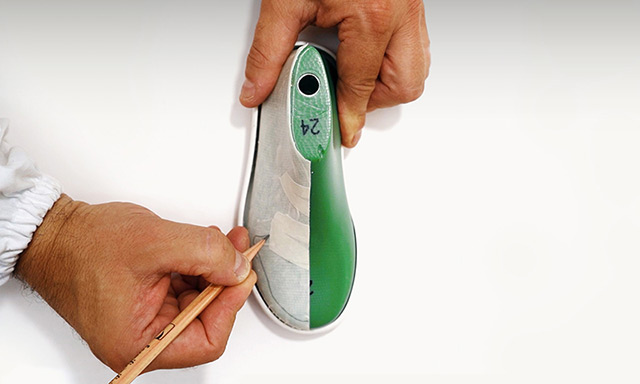
Pattern Cutting
The two-dimensional drawing is translated to a three-dimensional pattern by the pattern maker, the modellista. The result are cutting templates for each individual piece of the upper, laying the base for the material cutter. It is crucial that the conversion between sizes is flawless, a single error means the shoe will be warped and therefore not meet our standards.
Material Selection
A multitude of materials are used during the shoe construction process, each having their own unique benefits. Leather, although more expensive, is one of the only materials that assures both long-term wear and breathability, vital for good footwear.
Additionally, the natural leather we use is biodegradable, reducing the amount of waste significantly. It’s thickness is adapted to increase flexibility of the children’s shoe.
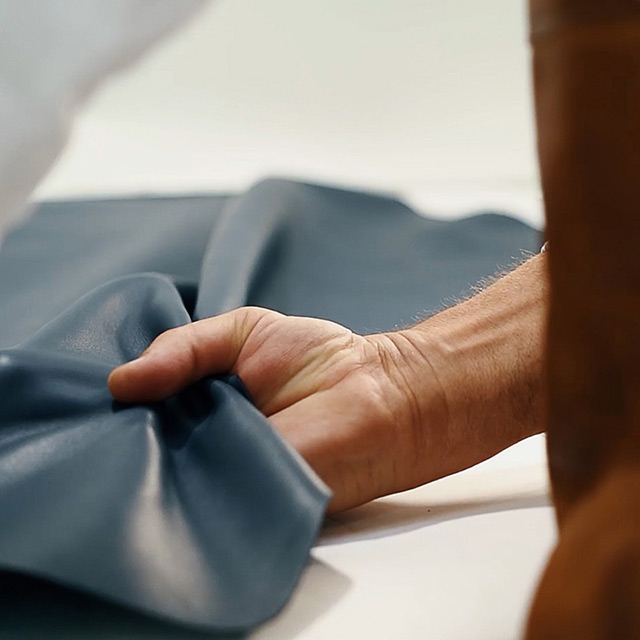
Leather is one of the most natural materials that can be used to craft shoes. Not only does it get a richer patina, colour, with age, the unique property of being both flexible and breathable is nearly unmatched. As an added bonus, it is entirely biodegradable if no plastic coating is added.
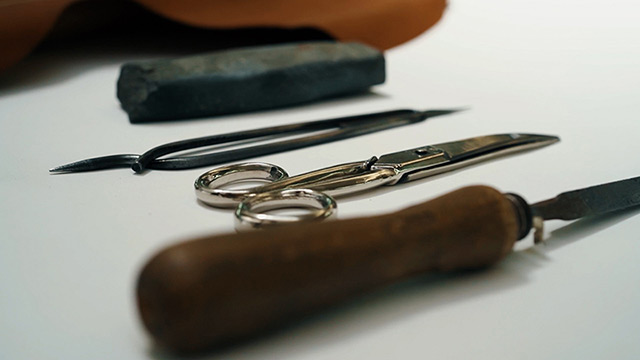
Leather Cutting
The material cutter, or tagliatore, checks every piece of leather carefully through stretching. Any natural defects are marked as to be avoided during cutting. Afterwards the patterns are placed on the leather in such a manner to avert any of the natural marks and to reduce waste before cutting. It takes numerous years of experience to develop an eye for this.
Highly skilled with his knife, he contours the patterns with a mesmerizing velocity. Additionally, pre-shaped pattern knifes are used with a press to cut through multiple pieces of material at once.
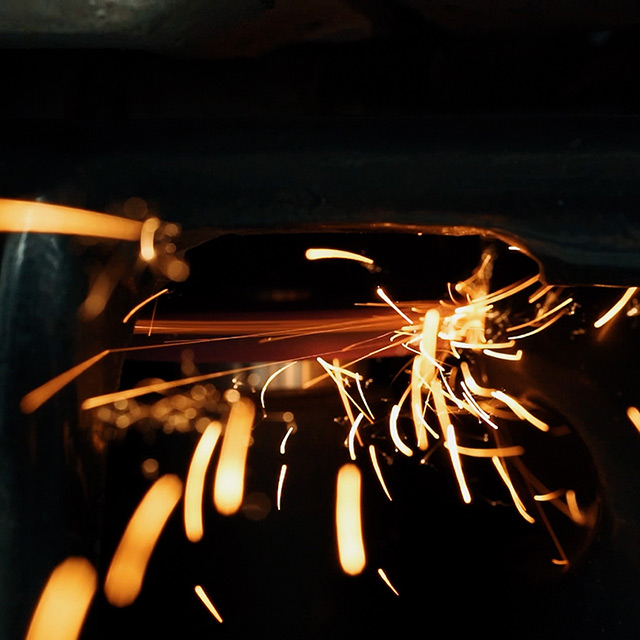
Skiving
The edges of the material is skived, meaning trimmed down in thickness. This is applied to areas where multiple parts overlap to make sure one panel transitions smoothly into the other. The result is a smoother and fluent upper. As material is removed in this process, there is no room for error.
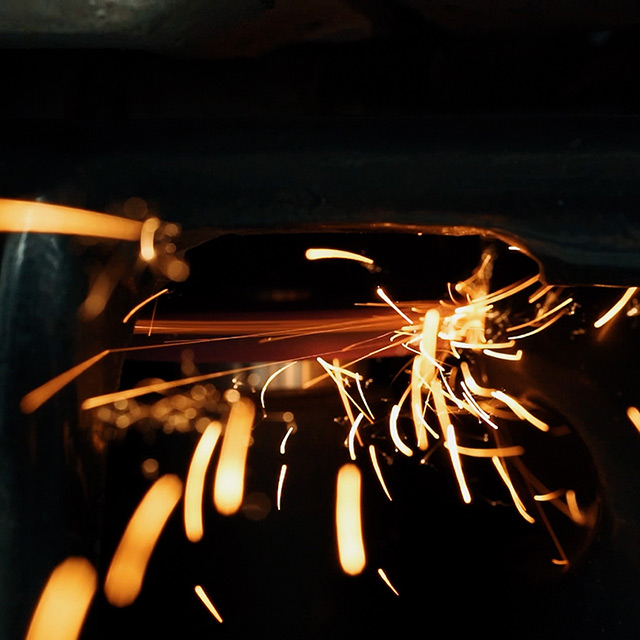
Stitching Upper and Lining
The different panels are bonded together along their skived edges by the stitchers, cucitrice. To assure breathability it is vital that a minimum of glue is used on the uppers. After attaching the panels with a light glue, they are hammered by hand to make sure they are secured together tightly and to maintain their shape.
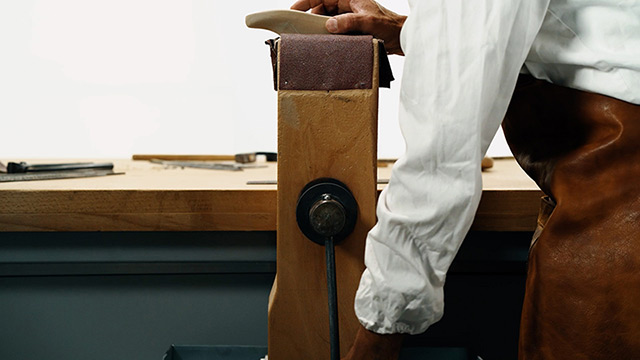
The Complication
During stitching, the process of guiding the needle through the different pieces requires great skill. A faulty stich often means the entire upper is rendered useless. Additionally, as our shoes are fully lined, a second layer is added on the insight and carefully folded over, once more with a minimum of glue. If applicable, lace eyelets are added one by one.
Shoe stitchers: One of the most delicate stitching processes is the stitching of leather shoes. It requires multiple years of experience to be fluent with the needle. A stitcher that is used to sewing clothing won’t be able to make a shoe without relearning the craft. People who are proficient in this art are becoming rarer every year.
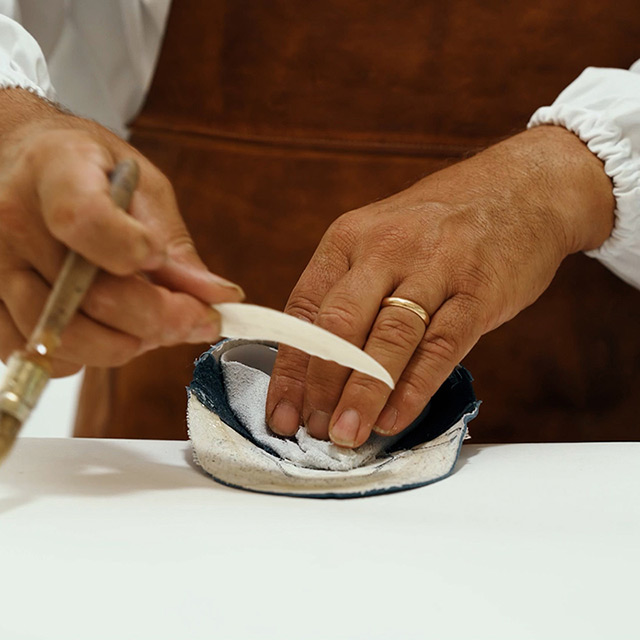
Reinforcements
To give support to the foot and maintain the shape of the shoe, reinforcements are added at the heel and toecap area in between the lining. The upper is then pulled over an ironing last, which is preheated, and pressed to fully shape the heel section and to iron out any creases.
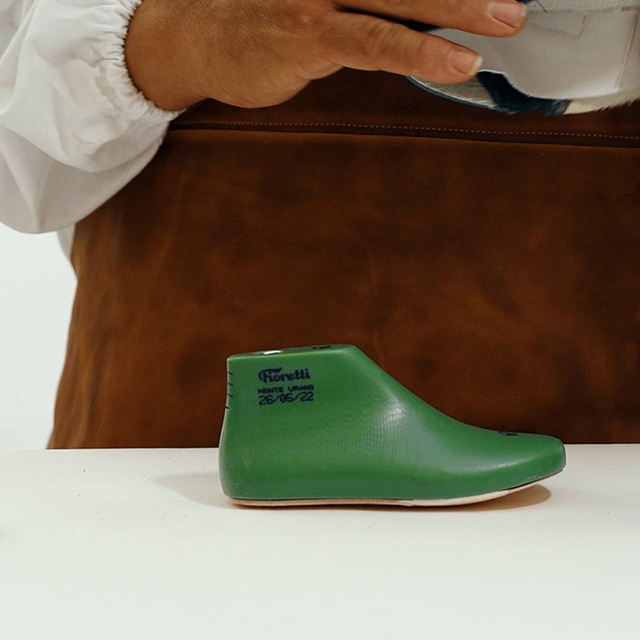
Upper Lasting
Once the heel has been shaped, the last is prepared with our Texon Flex midsole, a unique property of STONES and BONES shoes. After the midsole is nailed onto the last, the upper is pulled and stretched over the last, both by hand and machine. This shapes the shoe accordingly and prepares it for the soling stage.
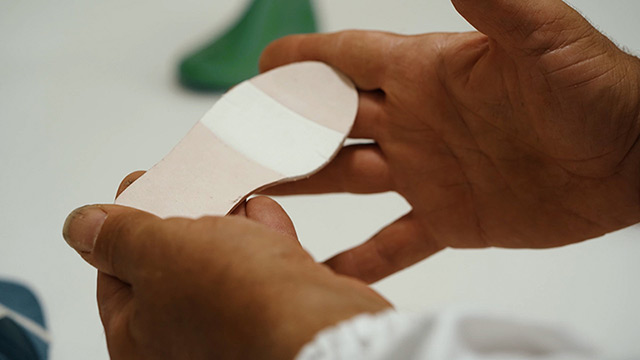
Flexible midsole: Introduced in children’s shoes by STONES and BONES, the Texon Flex midsole accommodates the bending of the foot in the right and natural location, around the ball of the foot. A shoe should not flex in the middle or at the heel area.
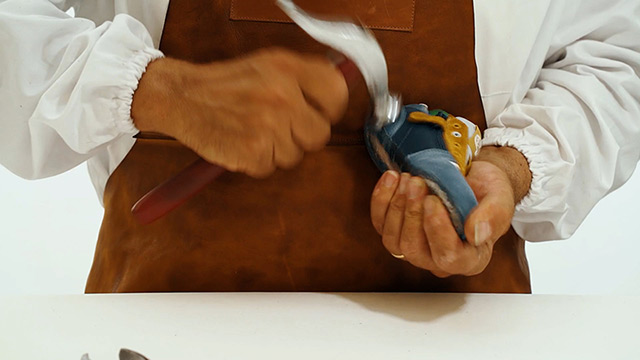
Sole Preparation
Before the sole is added, the bottom of the unfinished shoe is roughened, loosening the fibres. This makes sure the sole will adhere to the upper. Once again, the edges of the upper are skillfully hammered by hand to shape it even more to the last. Glue is applied to both the sole and the midsole and then activated with heat in a special oven.
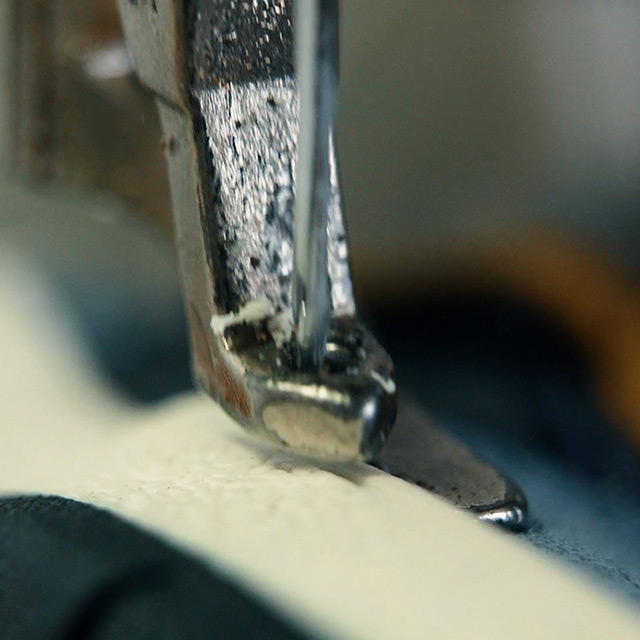
Marriage of Upper and Outsole.
Finally, the sole is married to the upper. Depending on the design of the shoe, only with glue or additionally with outsole stitching. Guided by hand, cup soles are stitched through both the upper and outsole, securing everything tightly together.
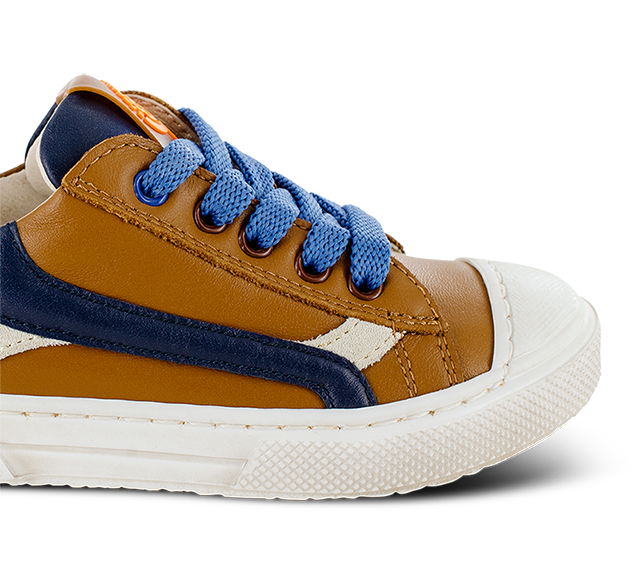
STONES and BONES cup soles: Most of the STONES and BONES cup soles have a reinforced toe area to protect the front of the shoe. Even though they are not indestructible, they can sustain more rough wear than our other types of soles and are perfect to accommodate the day-in day-out playing of children.
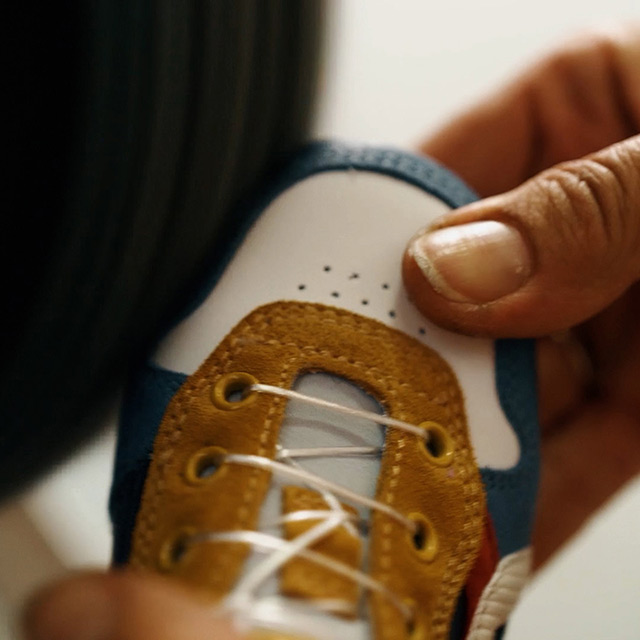
Brushing and Burnishing
To both enhance the esthetics and improve durability, the shoes are nurtured with natural creams and waxes at the finishing stage, or finisaggio, by the shoe shiner. Great depth of colour can be achieved by polishing and sometimes burnishing, the latter creating nuanced darker areas on the upper.
Polishing shoes: Polishing your shoes can not only prolong their lifespan, but also make them look almost brand new if done properly. Good quality leather allows for a unique and natural patina to develop as the shoes age.
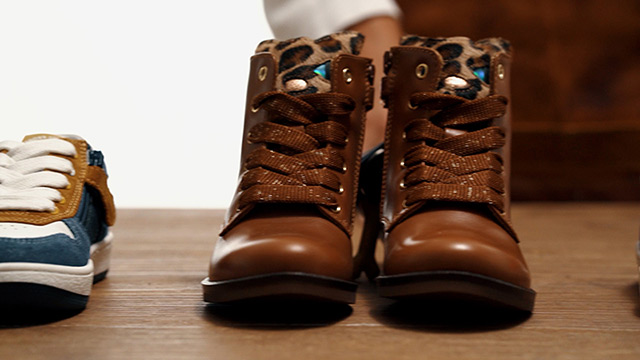
Finishing
Our unique vegetal tanned insole is added, with a latex cushion on the heel for extra comfort. Even though it seems quite stiff at the start, the reason why we use a leather insole is because after some time it starts to mimic the shape of the foot, creating a unique imprint which provides even more comfort over time as it becomes more subtle.
This is true for the entire shoe, over time leather starts to shape to the foot, providing an unparalleled support.
You can read more about our insoles here:
removable STONES and BONES insoles
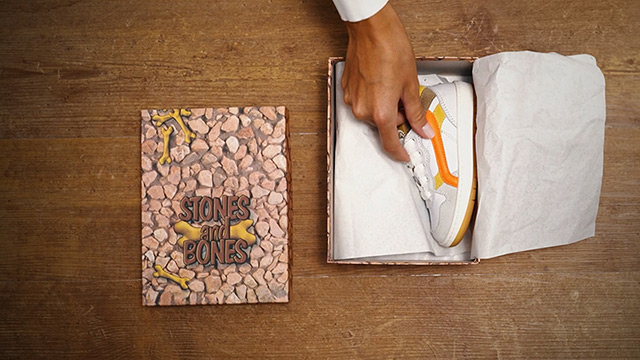
The Final Touch
Laces are added, a final clean and close inspection is carried out before the shoes are carefully wrapped in silk paper and placed in the STONES and BONES patterned shoeboxes, ready to be enjoyed by refined tastes.
In the end, there is always more than meets the eye when creating STONES and BONES shoes. Both passion and expertise flow throughout, culminating in unique designs and wearable creations, ready to be enjoyed by refined taste.